In the pulp and paper industry, compressed air is an essential element supporting every stage of the production process. A plant's compressed air system is therefore a major source of energy expenditure, and an important factor in its overall productivity and competitiveness.
Our customer, a maintenance manager at a paper mill in Quebec, had noticed that a compressor normally in backup mode was now running continuously, generating unusually high power consumption. The plant suspected the existence of significant leaks in the network, likely affecting the plant's economic performance, without being able to fully quantify the problem and its impact.
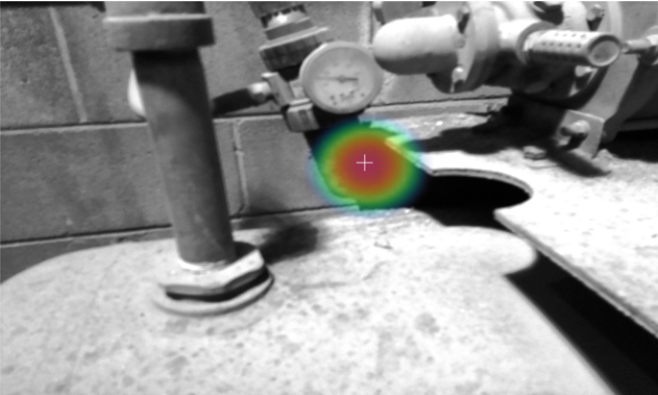
Revealing, identifying and quantifying the problem
We recommended to our customer an air leak audit by a technician specially trained in ultrasonic leak analysis using state-of-the-art equipment. Non-intrusive and relatively inexpensive, this method accurately detects compressed air leaks in the system and quantifies their volume. It requires no production stoppage and poses no risk to worker safety.
Our intervention revealed significant energy losses: 85 air leaks, mainly located at pipe junctions, were detected. A detailed report, accompanied by precise photographs, was given to the in-house maintenance team. Each leak was documented, enabling our customer to carry out the necessary repairs as part of their maintenance rounds in a targeted and efficient manner.
The results speak for themselves: the volume of leaks identified represents an annual loss of over 3 million kWh, costing $148,370 in unnecessary energy expenditure. With the report in hand, the plant now has the power to significantly reduce its electricity consumption and thus improve its environmental impact.
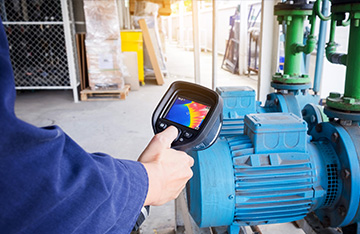
Benefits beyond the financials
Beyond the financial savings, this intervention illustrates the importance of a proactive approach to energy management. Knowing where air leaks are occurring and how much empowers a plant’s maintenance team to optimize the use of compressors that were constantly in support mode, reducing equipment wear and improving overall system performance.
The proposed solution offers several advantages:
- Accurate diagnosis without interrupting production
- Detailed report enabling targeted repairs
- Significant reduction in energy costs
- Minimized environmental impact
- Improved equipment durability
Would you like to optimize your plant's energy efficiency? Our team of experts is ready to meet your challenge.